Product news
Exact for Manufacturing Ease of Use: Picking materials for shop orders
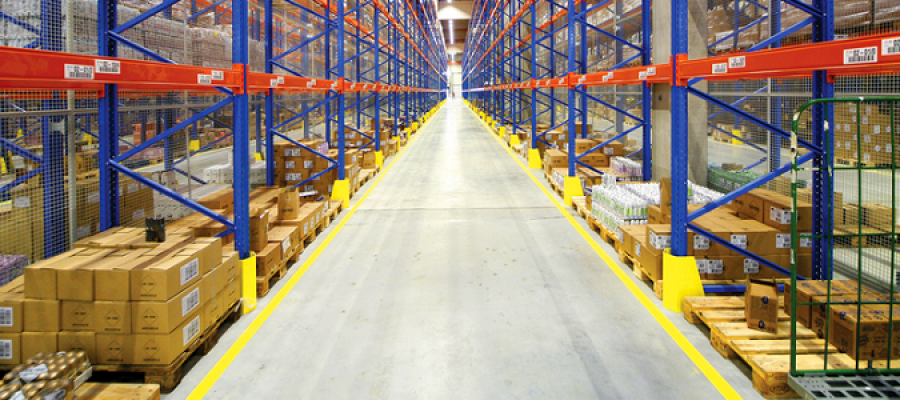
The person doing work preparation for the shop floor did have limited tools at hand to instruct the warehouse. The shop paper can be used for this purpose, but well known flaws are that all materials used are listed indiscriminately (order and stock controlled, subassemblies, backflushed), lines are not ordered by pick location, combined picking for multiple shop orders is not an option, and support for serial- and batch numbers is not provided. We are about to add three new layouts to reduce efforts for work preparation.
Layouts for manufacturing The various layouts for manufacturing (not including those for reversals, warehouse/location transfer and assembly orders) are depicted in this diagram. The new layouts are the Manufacturing Picking List, the Manufacturing Cluster Picking List, and the Shop Order Material Issue Slip:
Manufacturing Picking List The manufacturing picking list is an instruction to the warehouse to prepare materials of a particular shop order for issuing. It contains references to the shop order and a list of materials with their respective codes, descriptions, quantities, units and default pick locations. It is typically printed for open shop orders, i.e. before the start of the first operation. Printing a picking list does not affect the status of the shop order. The manufacturing picking list shows materials that should be collected in the warehouse like stock controlled materials, but will often exclude backflushed materials and (‘issue to parent’) subassemblies, both of which should be available on the shop floor. Manufacturing Cluster Picking List The manufacturing cluster picking list is an instruction to the warehouse to prepare materials of multiple shop orders for issuing. This reduces picking efforts. A manufacturing cluster picking list does not contain references to the individual shop orders. The process is to collect from the warehouse with a manufacturing cluster picking list, and then to prepare the individual issues from the collected items. Shop Order Material Issue Slip The shop order material issue slip is a confirmation of the materials issued to a particular shop order by the warehouse. It contains references to the shop order and a list of materials with their respective codes, descriptions, quantities, units, used pick locations and serial- and batch numbers. It is typically printed for open shop orders, i.e. before the start of the first operation, and the issue transactions will cause the shop order to change status to in process. The shop order material issue slip shows materials that are collected in the warehouse like stock controlled materials, but will exclude backflushed materials and (‘issue to parent’) subassemblies, both of which should be available on the shop floor. The order controlled materials are purchased on the shop order and with the purchase receipt a slip can be printed that serves as much as a receipt slip as well as an issue slip since the receipts are immediately issued to the shop order. Noteworthy about the shop order material issue slip is that it can serve as an instruction to the warehouse to pick serial- and batch number materials. As materials on an issue slip are no longer available to other shop orders, they have effectively been reserved which will avoid that batches are assigned twice. The Shop Order Material Slip is also useful when we don’t want to issue all material at once. We can simply set the quantities from the issue screen and print an issue slip as instruction to the warehouse. These improvements will become available in the next weeks for all versions of Exact for Manufacturing. The Ease of Use project aims to make Exact for Manufacturing easier and more efficient using the feedback of customers. Do you think we can make Exact for Manufacturing better? Contact Exact support and we dive into your suggestion.