Product news
Make flatter shop orders with phantom bills-of-materials
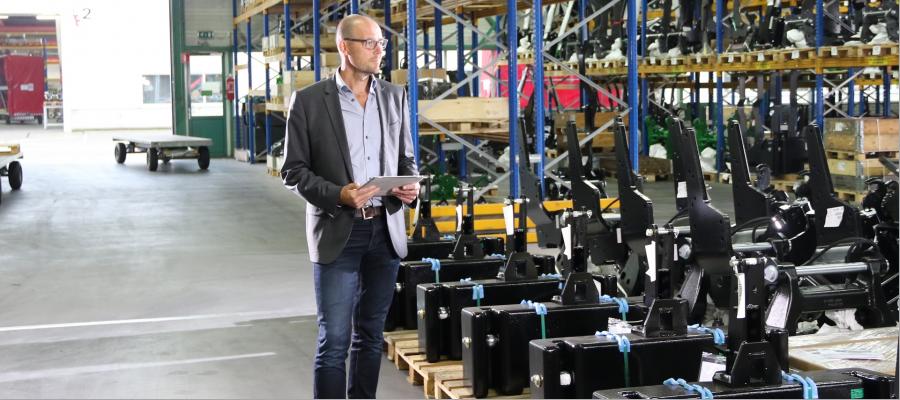
A common challenge with translating engineering bills-of-materials into manufacturing bills-of-materials is avoiding that they will result in shop orders with many suborders. While engineers and draftsmen are inclined to break down complex assemblies into many layers, manufacturing planners would prefer flatter structures that map the work on a particular work center into a single shop order or suborder. The phantom bill-of-materials is an excellent tool to achieve this.
Phantom-bill-of-materials
The word phantom-bill-of-materials may be new to you. APICS, the Association for Supply Chain Management, defines a phantom bill-of-materials as follows: “A bill-of-material coding and structuring technique used primarily for transient (nonstocked) subassemblies. A phantom bill-of-materials represents an item that is physically built but rarely stocked before being used in the next step or level of manufacturing.” A few examples will clarify what is meant.
A flat bill-of-materials will automatically result in a flat shop order
Suppose we maintain multiple bills-of-materials for what is basically the same bicycle: the green bike, the blue bike, the red bike, etcetera. The only differentiator between those bills is the color. We create a shop order for a green bike from the bill of a green bike. Easy, until we must maintain bills. For adding or removing parts, changing operations or by-products we will have to maintain the bills of each bike color separately. But, haven’t we just introduced functionality to replace materials in bills-of-materials? Yes. Unfortunately, we can’t add or remove materials and neither make changes to operations. So, this type of maintenance is cumbersome.
A potential solution that saves effort in the maintenance is mapping all common parts of the bicycle in a single bill-of-materials and refer to this common part in the bills of each bike color. A bike bill will then comprise of the common part plus the item for the paint color as a differentiator. However, the drawbacks are several: firstly there will be suborders generated for the common parts, driving us away from the objective to work with flatter shop orders. Secondly, the paint is required before the final assembly of the bike. So this solution incurs more problems than we like.
Now we introduce the phantom. In our implementation, the phantom bill-of-materials is not a property of the bill-of-materials version of the child, but a condition inserted in the line(s) of the materials of the parent. We can find the phantom condition in the calculator. By using the phantom, we automatically create flat shop orders while we can maintain the common part on one place only.
Phantoms are very useful in quoting for products with options
An example of a product with options is an oil pump. The customer can ask us to quote on a particular capacity pump, with a particular gear box and a control panel of choice. Of course we can venture into various configure-price-quote (CPQ) solutions offered by partners to manage just this. But if such a solution is just too advanced for this moment, the phantom can offer the right poor man’s tool. We start of by creating bills for each option: pump core “A”, pump core “B”, pump core “C”, gear box ”K”, gear box “L”, etcetera. When we enter the quotation, we insert the options of choice and upon receiving the customer’s confirmation we generate a shop order. Unfortunately, the result will be a shop order with various suborders for each option.
Now, let’s enter this quotation again, but now with applying the phantom condition to each option. The result is now a flat shop order:
Working with phantom bills-of-materials is supported in Exact Online Manufacturing Premium edition. This feature will be released in the third quarter of 2021.